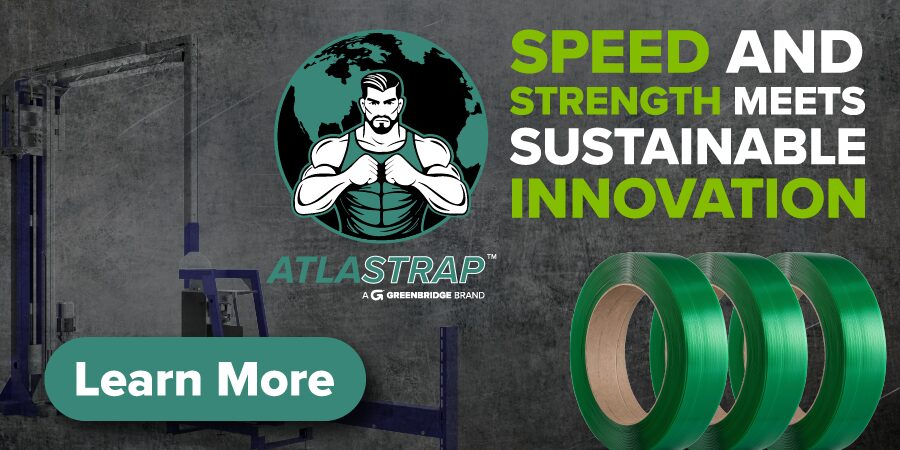
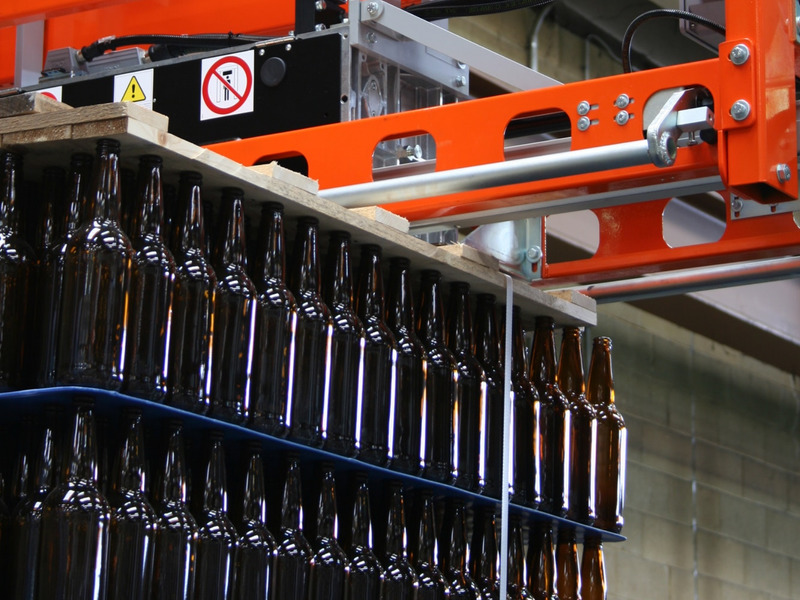
Five Things You Need to Know About Securing Cans and Bottles
A few years back, a plastic bottle maker called me late one afternoon hopping mad. A customer had given him with a few choice words about a load of bottles he’d just received. Opening the trailer, he expected to see neatly stacked pallets. Instead, empty bottles were everywhere. Turns out several pallets were disrupted in transit.
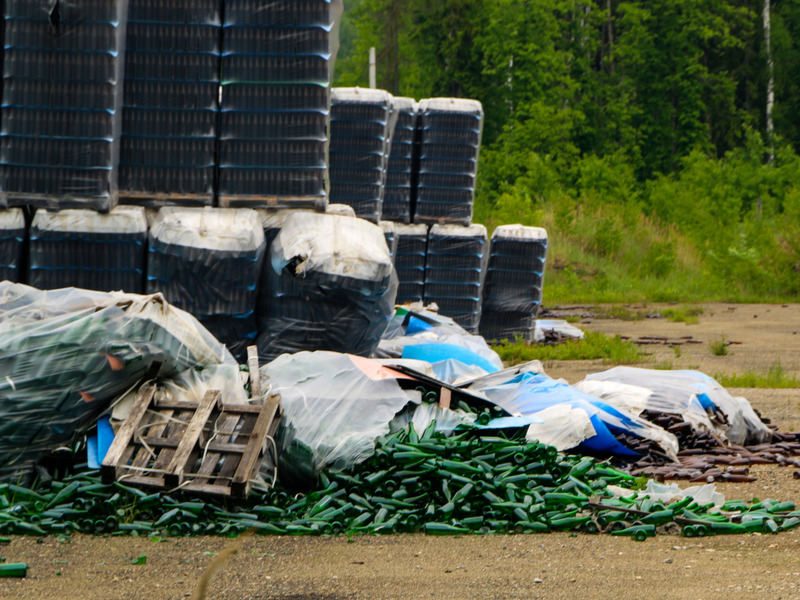
His customer sent the truck back. My customer had to rebuild the pallet loads by hand. He blamed the strap for the problem. And why shouldn’t he? The strap was loose on the failed pallet loads. Wasn’t it obvious that was the cause?
Actually, no. The cause of disrupted loads, the number one problem in the can and bottle industry, is not always obvious. In fact, it’s rarely obvious. Securing loads of empty metal cans, glass and plastic bottles and containers is far more complicated than simply stacking, stretch wrapping, strapping, and shipping. If only it were. There are a number of factors that go into securing a pallet load of empty cans and bottles so that the load successfully withstands the rigors of complex supply chains and arrives intact.
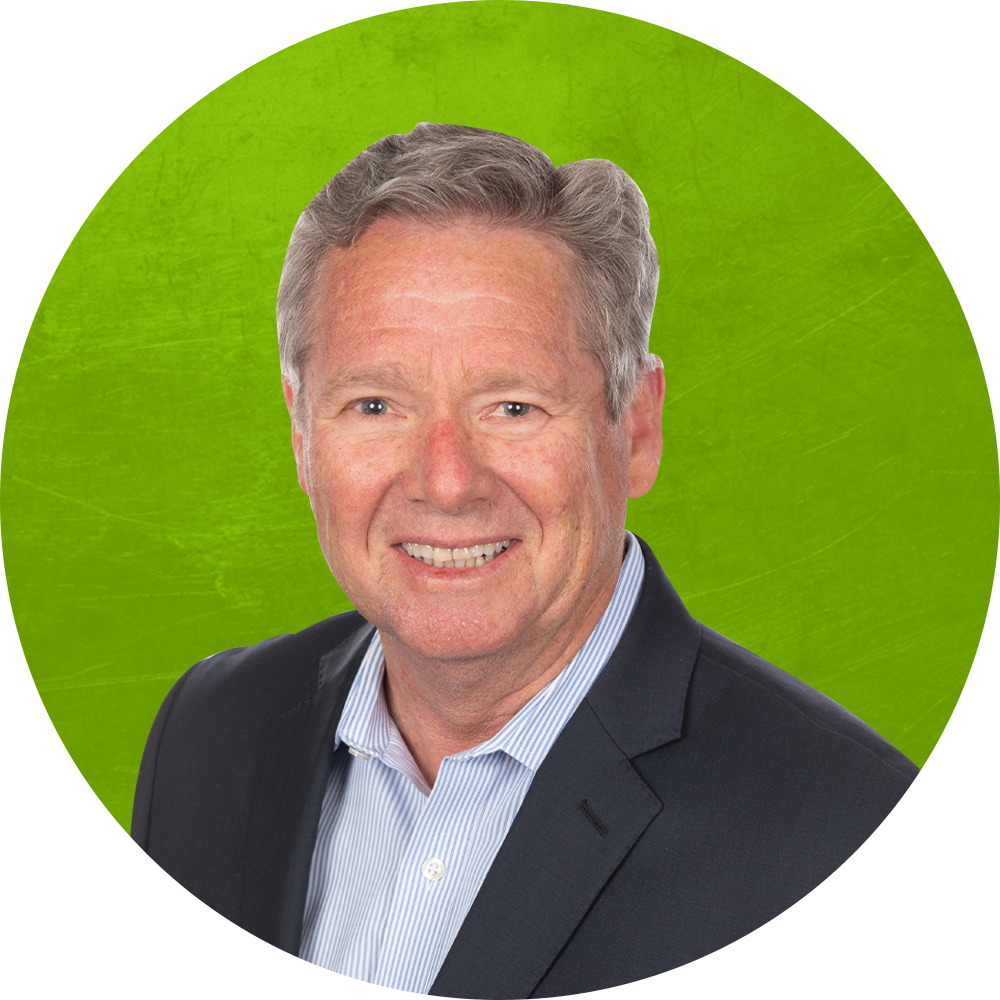
Over the 30 years of my career, I’ve come to know a thing or two because I’ve seen a thing or two. My protocol is: get on site with your customer to consult on the front end to provide a individualized load securement solution and trouble shoot on the back end if there’s an issue. In the case of the guy I just mentioned, I got to his plant pronto, and determined a palletizer was building leaning Towers of Pisa, which then failed on the road. Problem solved; strap absolved.
That’s not to say strap is perfect. It’s not. But it does underscore that disrupted loads are caused by a number of variables, many of which can be avoided. For this reason, I’ve put together the Five Things You Need to Know About Securing Cans and Bottles. Here goes…
ONE: Unique Securement Challenges
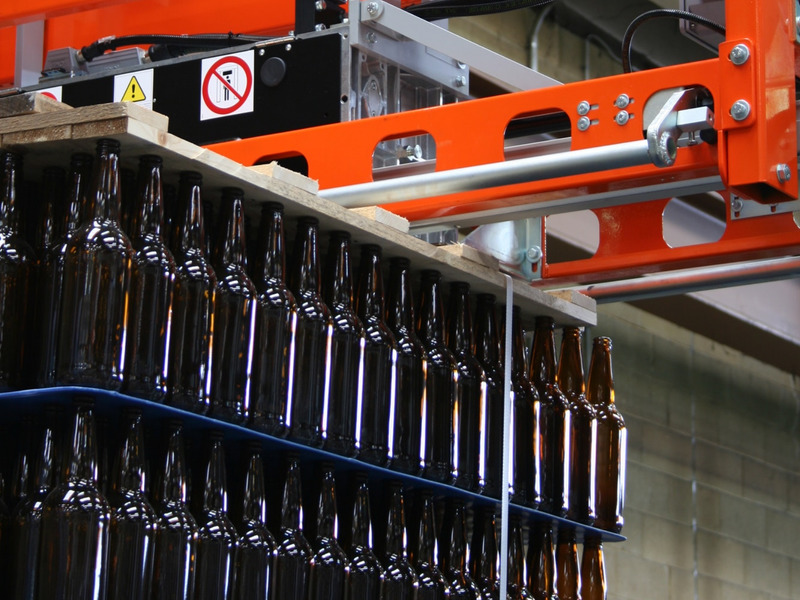
Trust me on this: empty containers can be extremely difficult to secure. Each category—PET bottles, aluminum and steel cans, glass bottles for beer and wine – has its own set of quirks. For example, a 16-ounce PET water bottle can weigh as little as 19 grams, about half an ounce. Securing multiple layers on a pallet is a feat of engineering. You really have to fine tune the strap tension to apply without crushing the lightweight bottles. Contrast that with glass bottles, which require a far higher amount of tension to secure. The only format I’ve found to be easy to secure is glass food jars. They’re a walk in the park.
Takeaway here is you have to understand the inherent challenges of the package itself before you do anything. And that’s just a start. Next!
TWO: Pallet System
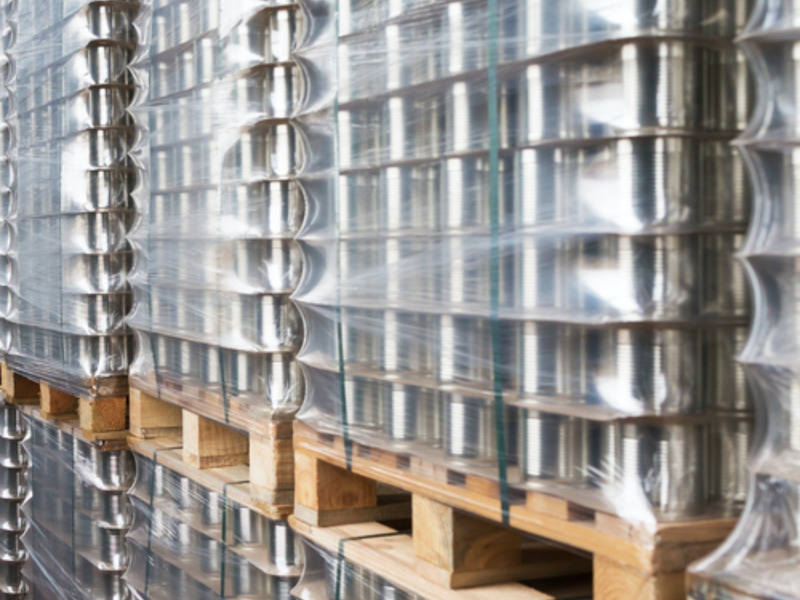
Way back when, can and bottle makers all used wood pallets and disrupted loads were a rarity. Now, with many companies moving to plastic pallets, disrupted loads are more common. Why is that? In a nutshell, wood is inherently more forgiving than plastic. When you pull tension on a load of bottles on a wooden pallet, the wood “gives” to the pressure, which helps give the strap something to “grip” and stay tight. Also, when using wood pallets, fiber slip sheets are placed between each layer. Like wood pallet, fiber slip sheets are forgiving, allowing bottles to nestle into the paper-based sheet. The load is finished with a wooden top frame and strapped, making for an overall package that stays secure across the supply chain.
Plastic pallets have become increasingly popular in recent years due to their reusability and extended use life. The system includes plastic slip sheets and a plastic top frame. It makes for a very tidy, clean package. With plastic; however, the dynamic changes. Plastic pallets are typically made of HDPE and as such are rigid and don’t give when strapped. Likewise, the slip sheets don’t conform to the bottles. Top frames are also rigid. The tension dynamics are very different from wood. Instead of absorbing energy, the plastic pallet system pushes energy out rather than straight down, which is what happens with a wood pallet. This makes loads on plastic pallets more difficult to secure. This is not to say plastic pallets can’t be secured—they can. What it does mean is we need to accommodate the material and take a different approach to strap application and strap tension Accommodating the unique differences of wood and plastic pallet systems on the front end pays dividends on the back end.
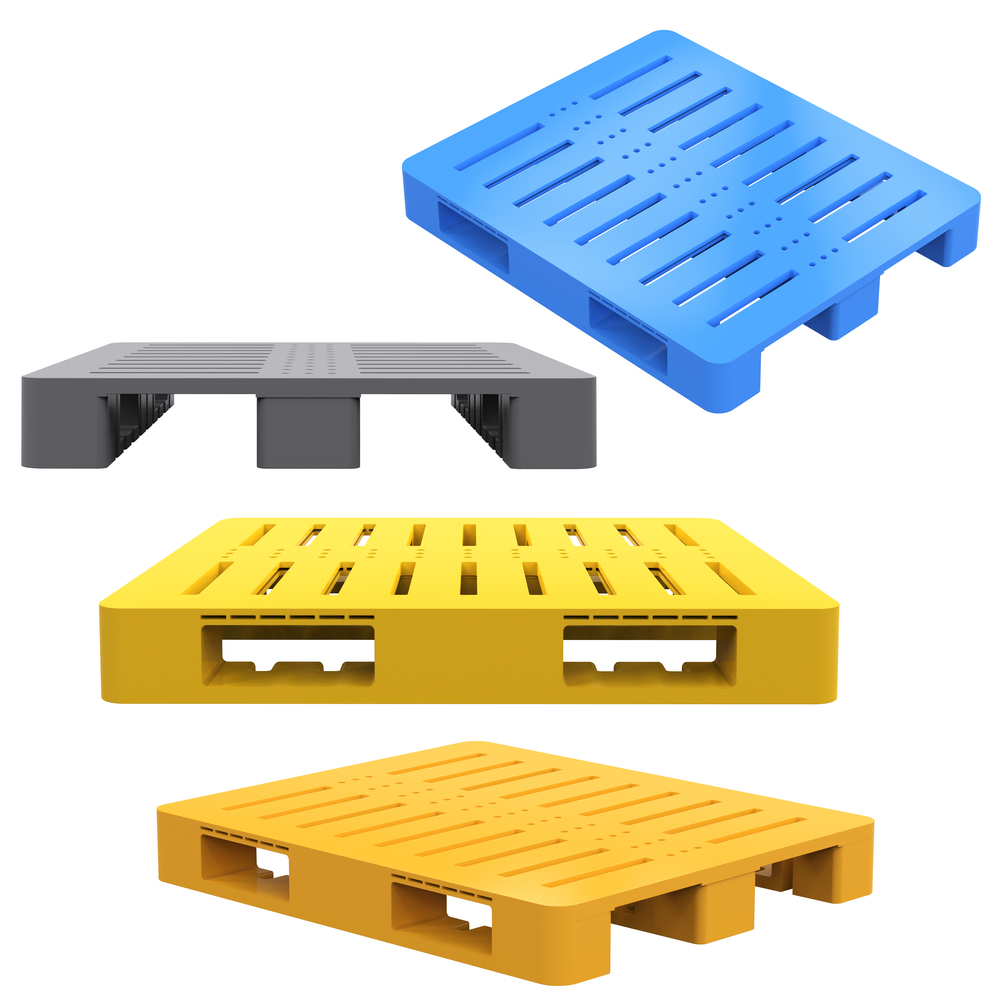
Right now, PET bottles and aluminum cans are largely shipped on plastic pallets. Steel cans and glass bottles and jars are split 50-50 between wood and plastic. Smaller breweries, distilleries, food and beverage makers are the biggest users of wood pallet systems due to the higher cost of plastic pallets. This is not to say one system is better than the other. Understanding the differences and adjusting how you strap are key. But hey, there’s more to securing a load of cans and bottles than the pallet system…
THREE: Warehousing
Your cans and bottles are palletized, strapped and ready to go. Or are they? It all depends on a number of warehouse-related variables. One of the first things I ask customers is how long they keep loaded pallets in their warehouses. There are several reasons for this question. First, strap can lose 40% of tension in first 24 hours of being applied before leveling off. If you keep a 15- to 30-day supply of product in your warehouse ready to ship, just imagine how this impacts the integrity of your pallet loads. Length of time in the warehouse must be taken into account when the load is initially strapped.
The second thing to consider is how high your pallet loads are stackd. Typically, it’s two to four pallets high. When determining how best to secure your pallet loads, we need to consider the stress placed on the bottom pallet and its contents. Time in warehouse and stack height both help determine the proper tension of your strap. There’s another aspect of warehousing we can’t forget…
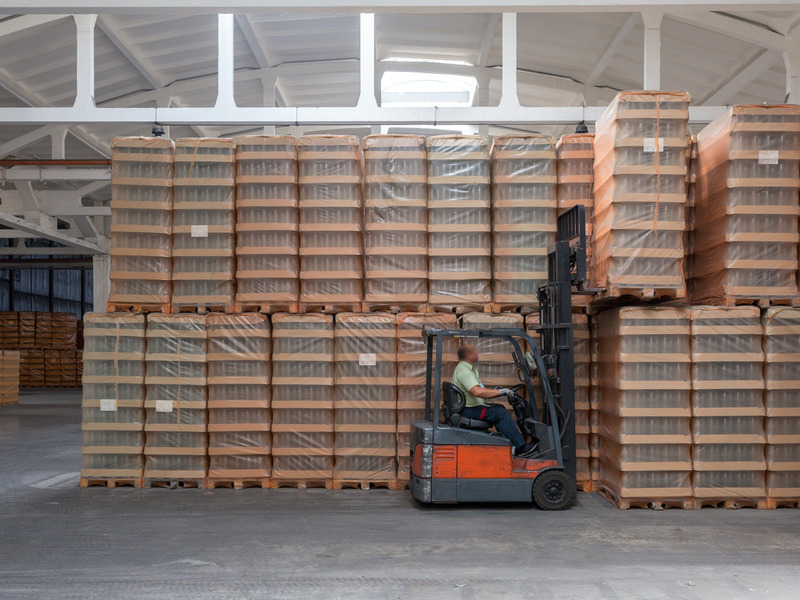
FOUR: Handling
I don’t care how secure your pallet loads are, they won’t survive a reckless forklift or clamp-truck driver. And I’ve seen some guys drive like the Indy 500—fast and tight around the curves. Others are like bumper car drivers. Make sure your handlers respect their loads from the production floor to the loading dock. It matters.
FIVE: Transit Conditions
The final thing you need to know is how transit conditions affect your load integrity. Let’s start with your trailers. The inside of a trailer is like a seesaw. At the front of the trailer, there’s very little movement so pallet loads are stable. The back of the trailer is entirely different. Every bump, every pothole, every curve in the road will be felt differently by loads in the back. To ensure a smooth trip, you want to make sure you fill any void, front and rear, with airbags to prevent excess movement or impacts that can disrupt the load. Other considerations are length of the trip and road conditions. Short trips over smooth interstates are a cinch. Long hauls with more difficult terrain—imagine steep grades and winding mountain roads—and you get the picture. Strap can get really stressed in certain conditions.
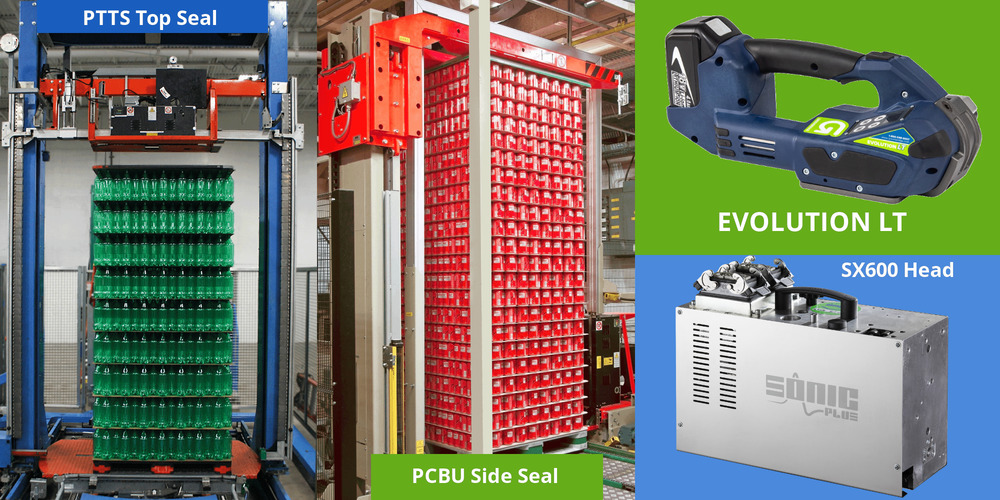
There’s a Lot that Goes into Properly Securing Cans and Bottles for the Long Haul
As you can see, a lot goes into getting your cans and bottles from A to B intact. Which is why Greenbridge has always taken a technical, consultative approach to customers’ load securement needs. As I mentioned earlier, I like to get with customers on the front end—not to sell strap but to understand what you’re facing so we really get our arms around what you’re going to need in terms of straps per load, initial tension, retained tension, and load compression. We will recommend the proper equipment, tools, strap, and accessories like cornerboard. We’ll even train your people on proper strapping techniques. Training can be done live or we can schedule virtual training through our Load Securement Center of Excellence in Green, Ohio.
Finally, I’ll conduct strap tests at customer sites where we dial in on the product, tension and other variables. When we get through, you’ll know your loads are properly secured.
I hope this has been helpful. If you’d like to learn more about Greenbridge’s Can + Bottle Load Securement Solutions that include PET strap, cornerboard, equipment, heads, and tools, check out our new brochure here. You can also connect with the Greenbridge Technical Sales Team here.